A guide to supply chain control tower use cases
Jul 06, 2023 • 11 min read
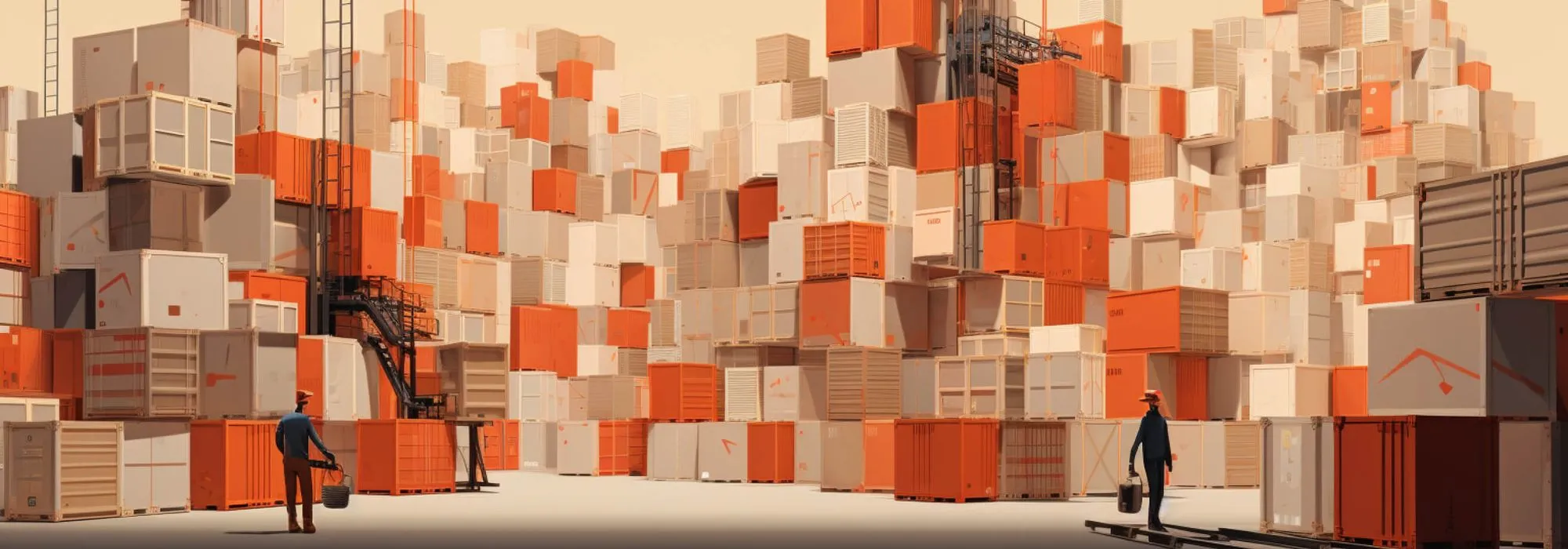
The quality of various strategic and tactical decisions, such as capacity planning, supplier selection, and inventory ordering, directly influences the efficiency and resilience of a supply chain. Limited visibility into various stages of the supply chain, insufficient data availability, and lack of analytics and optimization tools can lead to detrimental consequences in the form of stock-outs, excessive shipping costs, and lost customers.
To ensure flawless and efficient supply chain operations, many retail and manufacturing companies implement a centralized system that consolidates the data across all stages of the supply chain, continuously evaluates risks, performs optimizations, and helps teams to react rapidly to disruptions. Such a system is often referred to as a supply chain control tower.
In this blog post, we showcase a functional blueprint of a control tower for an inbound supply chain. We discuss the fundamental capabilities such a system should provide, and the specific use cases it should support. This blueprint can be implemented using a combination of proprietary products, cloud-native services, and custom applications, which we discuss at the end of the article. At a high level, we assume that the control tower receives a broad range of data from 1st and 3rd parties, and integrates with a number of operational systems, such as the system for warehouse management, and provides four categories of capabilities:
- Strategic planning. Decision support tools that are focused on long-term, often multi-year, time horizons.
- Inventory visibility. Near real-time insights and alerts that support ongoing operations.
- Inventory flow control. Decision automation tools for ongoing operations such as replenishment.
- Impact analysis and resolution. Tools for reacting to disruptions and deviations from planned scenarios.
This layout is summarized in figure 1 below. This diagram also includes the supply chain model which represents the supply chain topology and its key parameters. In the following sections, we develop more specific designs for each of the above categories.
Strategic planning
The strategic planning tools provided by the control tower aim to evaluate and mitigate risks and inefficiencies associated with product design decisions, choice of suppliers and partners, network topology, and revenue model.
Revenue-at-risk analysis
The assessment of supply chain risks often starts with evaluating the revenue contributions of products, parts, and suppliers. This process is often referred to as the revenue-at-risk evaluation. The goal of this analysis is to get a quantitative picture of which inventory items and categories need to be protected the most based on their revenue contribution. The following example shows what the revenue-at-risk dashboard can look like:
The revenue-at-risk values and their contributions (percentages of the total revenue) can change over time, so the analytics tools usually support historical data visualization and forecasting of the revenue values:
Design and supplier optimization
The revenue-at-risk assessment is followed by the development of mitigation strategies. In particular, the company can change suppliers of certain parts or modify product designs to reduce the risks. Such decisions are supported by risk evaluation tools that allow one to assess the current risks and perform what-if analysis for alternative scenarios.
An example interface of a risk evaluation tool is outlined in the figure below. The tool uses part/supplier attributes, external data and expert ratings, such as geopolitical risk indicators, and historical data such as the observed lead times, to evaluate the risk of disruption (or, alternatively, undisrupted supply) on a time horizon from several months to several years. These estimates (survival curves) can further be aggregated to the product level and inform product redesign activities and supplier selection.
Inventory visibility
The tactical supply chain planning and optimization activities require accurate near-real-time inventory data to be available. Collecting, aggregating, and sharing this information is not a trivial problem, and requires creating a scalable master data management system and services for computing inventory statuses and acting on their updates.
Global visibility and reporting
One of the biggest challenges associated with inventory visibility is the collection and consolidation of data across all stages of the inventory lifecycle, such as supplier backorders, on-order inventory, in-transit inventory, on-hand inventory, returned inventory, and more. This generally requires integration with supplier systems and data feeds, enterprise resource planning systems (ERPs), third-party logistics partners (3PLs), warehouse management systems, and other event sources. The raw inventory information can be used to provide basic insights into the current situation, as shown in the figure below, as well as enabling more advanced capabilities described in the following sections.
The main KPIs that are tracked by the supply chain visibility and reporting services include the following:
- On-time to Request. The ability to deliver products in full on or before the date requested by the customer.
- On-time to First Promise. The ability to meet the shipment date committed by the company to meet the requested quantity in full.
- On Time In Full (OTIF). Measures order fulfillment accuracy. To calculate the OTIF ratio, take the orders that were fulfilled accurately (on time and in the right quantity).
- Months of Supply. Measures inventory on hand to service demand for a defined time period.
- Open POs. Number of in-progress procurement orders.
Availability services
The raw inventory data usually needs to be transformed into derived statuses and attributes that can be consumed by eCommerce services, order management systems, and other downstream applications. A canonical example of a derived attribute is available-to-promise (ATP), which refers to inventory levels that a company can commit to selling. Computing ATP generally requires taking into account in-transit and on-hand inventories, their locations, existing customer orders, requestor details, and other pieces of information. The ATP computing logic can include the fair share rules for arbitrating the situations when the demand exceeds supply, and other business logic.
The services that make derived statuses available to downstream applications can also provide suggestions on the optimal inventory sourcing locations, provide the ability to make inventory reservations, and support other features:
Smart alerts
The information consolidated in the global inventory database can be used to monitor ongoing operations, and detect risks and disruptions. The main types of risks monitored by the control tower include procurement risks (tier-1 or tier-2 suppliers are not able to fulfill the orders), scheduled receipt risks (shipping disruptions such as tornadoes), capacity risks (running out of storage or production capacities), and demand risks (unexpected demand spikes or drops). These risks can be monitored using rule-based and statistical methods that raise corresponding alerts when risks are identified:
The alerting service can use a broad range of signals, over and above the core inventory data, to detect disruptions in early stages. Examples of such additional signals and supply chain data sources are as follows:
- In modern supply chains, IoT plays an important role in supply chain visibility and alerting. The control tower can receive alerts from connected devices at factories and connected vehicles to detect production and transportation disruptions in early stages.
- The control tower can use advanced analytics methods such as large language models (LLMs) to analyze news feeds and evaluate their impact on the supply chain.
Inventory flow control
Operating a supply chain requires continuously procuring and routing inventory through a network. In this section, we discuss the services that manage and optimize inventory flow, preventing stock-outs, and reducing storage and shipping costs.
Demand sensing and forecasting
Efficient inventory flow management requires accurate demand forecasts to be available. These forecasts generally need to be produced for multiple levels of granularity (e.g. SKU x Channel and SKU x Store), multiple time horizons (e.g. long-term planning and operational), and multiple purposes (e.g. assortment optimization and price optimization). Consequently, designing a forecasting solution is often a challenging task that requires efficiently covering all necessary use cases and features with a small number of models and forecasting processes.
One important aspect of this problem is the ability to incorporate various external factors and signals into the short-term operational forecasts. Examples of such signals include competitor promotions, weather forecasts, and ongoing macroeconomic conditions. Creation of such short-term forecasts is often referred to as demand sensing, and is separated from long-term forecasting, which puts more emphasis on seasonality and trends:
Inventory allocation and replenishment automation
Demand forecasting enables the optimization of inventory levels across network nodes. This is usually a complex procedure that takes into account the expected demand, storage costs, shipping costs, and many other factors and constraints to minimize the overall operational costs and improve the SLAs.
The inventory optimization procedure can be executed in several different modes depending on the industry and the type of merchandise. One typical scenario is the allocation of seasonal inventory: an apparel retailer that procures non-replenishable merchandise before the season can execute the optimization procedure to determine the optimal stock level for each supply chain node, procure, and allocate accordingly. On the other hand, a retailer that sells replenishable products can use the optimization procedure to determine the target stock levels at each node, and then continuously review and replenish the inventory up to this level:
Impact analysis and resolution
As we discussed in the previous sections, the supply chain control tower typically monitors the global order, shipping, and inventory data, and generates alerts when disruptions or risks are detected. In this section, we discuss tools and services that facilitate the downstream analysis and troubleshooting of these alerts.
Inventory rebalancing
Procurement, shipping and capacity issues often result in stock-outs and order fulfillment delays. The first capability that is critical for troubleshooting these issues is the impact assessment, so that the orders and locations impacted by the disruption can be quickly identified, and the impact timing and magnitude can be accurately estimated. The second capability is resolution planning. One of the most powerful methods for resolving the main types of disruption, including demand surge, production disruption, and in-transit disruption, is inventory rebalancing across the nodes which aims to restore the disrupted balance between the supply and demand. The control tower should provide services for automatic creation and evaluation of rebalancing plans, similar to the interface outlined in the following figure:
Supplier collaboration
Besides inventory rebalancing, collaboration with the risk-prone suppliers or alternative vendors is an important part of the resolution process. The control tower can provide services and integrations for communicating with suppliers and collaborative resolution of shipping delays and other issues:
Integration with other systems
The control tower usually integrates with a number of systems and workflows that address other aspects of supply chain operations. The most essential integrations include the following:
- Demand shaping. Inventory rebalancing and collaboration with suppliers is a powerful way to resolve disruptions, but many supply issues can also be addressed by making adjustments to sales and distribution processes. For example, inventory shortages can be addressed by increasing prices, reducing promotional activity, or prioritizing orders and customers. These adjustments are collectively referred to as demand shaping. The coordination between supply management processes and demand-shaping activities is a powerful way to improve supply chain resilience and service levels.
- Order sourcing. The inventory visibility services are closely integrated with the order management systems (including external and internal orders) so that up-to-date inventory data is used to make optimal order sourcing decisions, and, conversely, the ongoing orders and reservations are used to update the inventory statuses.
- Warehouse and transportation management. Finally, the inventory visibility services integrate with the warehouse and transportation management systems to incorporate reception and inventory counting updates, and execute rebalancing decisions.
Implementation strategy
The supply chain control tower capabilities are typically implemented using one of the following three strategies:
- Supply chain management products. Major vendors of supply chain management software, such as Blue Yonder and O9, provide specialized control tower products, or offer multiple products that collectively cover control tower functionality.
- Specialized services from major cloud providers. Microsoft Azure and Amazon Web Services (AWS) currently offer supply chain management services that partly cover control tower functionality.
- Custom solutions. Large retail and manufacturing companies often choose to implement custom control tower solutions that provide capabilities beyond off-the-shelf products.
The choice of implementation strategy is influenced by many factors, including the industry and size of the business. For example, manufacturers of complex products, such as electronics, often sign up for building advanced custom solutions for supply risk evaluation and mitigation, and large retailers with a complex mix of physical and digital sales channels often develop custom availability services to operate these channels in a consistent and efficient way.
Conclusion
In this article, we described a collection of services and capabilities that enable efficient supply chain management and resilience. These services do not necessarily need to be implemented as a single system or platform, but many companies choose to consolidate them into one logical entity called a supply chain control tower. The advantage of this approach is a strong focus on comprehensive disruption detection, prevention, and resolution that is enabled by consistent and flawless data collection, analysis, and operationalization.
Interested in a supply chain control tower for your organization? Contact us to start a conversation with our supply chain optimization experts.
FAQs
How does a control tower impact each level of the supply chain?
A supply chain control tower can have a significant impact on each level of the supply chain by enhancing visibility, collaboration, and decision-making. It acts as a central hub that provides real-time data and analytics, enabling better coordination and optimization across the entire supply chain ecosystem.
At the operational level, a control tower allows for improved visibility into various stages of the supply chain, including inventory levels, production schedules, and transportation status. This visibility helps to identify and address potential bottlenecks or disruptions promptly, minimizing stockouts and delays. By having a comprehensive view of operations, companies can make data-driven decisions and adjust their plans accordingly, leading to increased efficiency and reduced costs.
At the tactical level, a control tower enables better collaboration among different stakeholders, such as suppliers, manufacturers, and distributors. It facilitates the sharing of information, forecasts, and plans, allowing for synchronized decision-making. This collaborative approach helps to optimize inventory levels, align production capacities, and streamline transportation routes, leading to improved resource utilization and reduced lead times.
At the strategic level, a control tower provides valuable insights and analytics that support long-term planning and decision-making. By analyzing historical and real-time data, companies can identify trends, forecast demand patterns, and optimize their supply chain network design. This enables them to make informed strategic decisions, such as selecting the most efficient suppliers, establishing strategic partnerships, or expanding into new markets.
What are the costs of a supply chain control tower?
The costs associated with implementing and operating a supply chain control tower can vary depending on several factors, including the size and complexity of the supply chain, the scope of functionalities required, and the chosen technology and implementation approach. Here are some cost considerations:
- Software and technology: Acquiring or developing a supply chain control tower software solution can involve upfront costs, licensing fees, or subscription costs. The complexity and features of the software can influence the price. Additionally, there may be costs associated with integrating the control tower software with existing systems and data sources.
- Infrastructure and hardware: Depending on the chosen deployment model, such as on-premises or cloud-based, there may be infrastructure and hardware costs involved. This includes servers, networking equipment, and storage infrastructure. Cloud-based solutions often involve monthly or annual subscription costs.
- Implementation and customization: Implementing a control tower requires configuring the software to align with the company’s specific supply chain processes and requirements. Implementation costs may include consulting fees, system customization, data migration, training, and change management.
- Data integration: Integrating various data sources from within the organization, as well as external partners and suppliers, may require additional investment. This can involve data mapping, API development, data cleansing, and data integration tools or services.
- Personnel and expertise: Operating a control tower may require dedicated personnel, such as supply chain analysts or control tower managers, to monitor and analyze the data, make informed decisions, and drive continuous improvement. The costs associated with hiring, training, and retaining skilled personnel should be considered.
- Maintenance and support: Ongoing maintenance, updates, and technical support for the control tower software and infrastructure may involve recurring costs. This ensures the system remains up-to-date, secure, and compatible with evolving technologies
- It is important for companies to conduct a thorough cost-benefit analysis, considering both the initial investment and the potential long-term benefits, such as improved efficiency, cost savings, and enhanced decision-making capabilities. The costs of a supply chain control tower can vary significantly depending on the specific requirements and circumstances of the organization.
Tags
You might also like
The buzzword “composable commerce” has dominated digital strategy conversations since Gartner popularized the term in 2020. But behind the marketing hype lies a longstanding, proven practice of integrating specialized, best-of-breed technology components into a flexible and scalable ecosystem....
In today's fast-paced and data-driven world, accurately predicting demand is more critical than ever for businesses aiming to stay competitive. Traditional forecasting methods often provide a single-point estimate, which can be useful but falls short in accounting for the inherent uncertainties and...
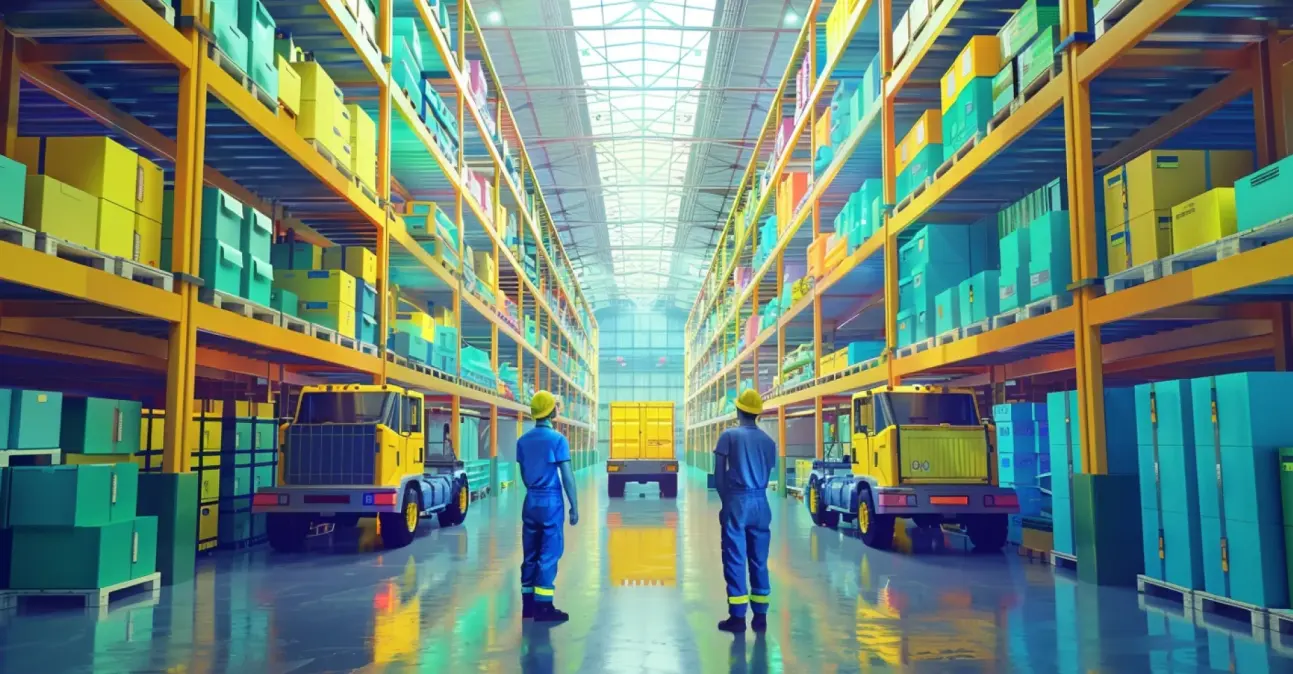
During the pandemic, many manufacturers encountered sudden demand shifts and supply chain disruptions, affecting everything from raw materials to finished products. And until recently, the Baltimore port incident triggered widespread delays in cargo handling, affecting industries from automotive to...
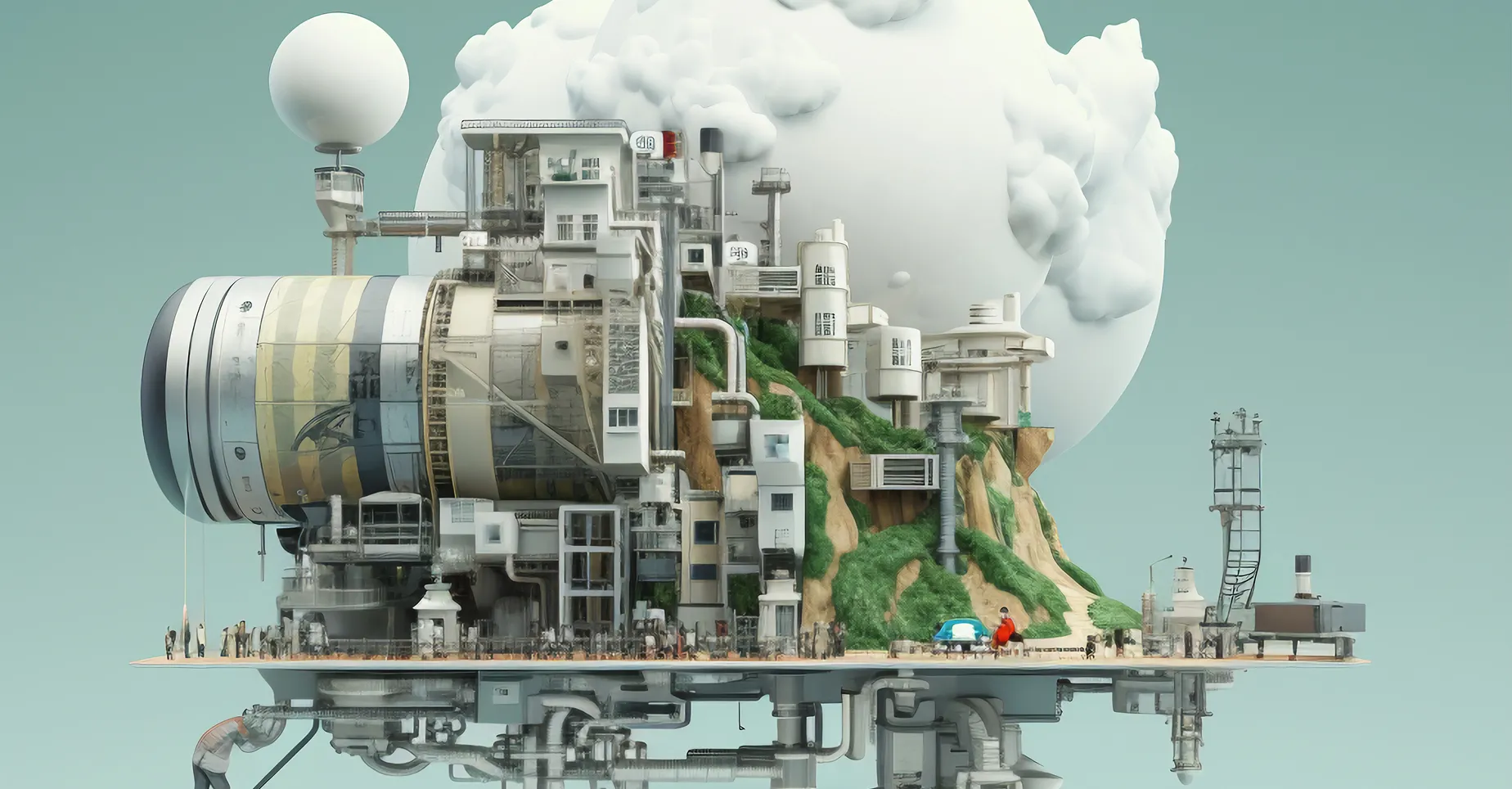
Contract manufacturing involves outsourcing production to third-party manufacturers, which allows companies to focus on core competencies such as design, branding, and distribution. The global contract manufacturing market was valued at USD 246.51 billion in 2022 and is expected to reach USD...
Demand forecasting is a crucial aspect of retail supply chain management that involves predicting future customer demand to make informed decisions about inventory levels, production, and resource allocation. It is a statistical analysis that considers numerous variables to optimize the predict...
In the ever-evolving landscape of transportation, modern Electric Vehicles (EVs) and Hybrid Electric Vehicles (HEVs) have transcended traditional notions of mobility. Beyond mere modes of transportation, these vehicles have emerged as platforms for innovation, where cutting-edge technologies redefi...
Recent sustainability legislations and regulations make due diligence a business imperative for effective supply chain management. Increasingly, regulations and local government bodies are regulating how enterprises must approach, operate, and report on their supply chain operations, both directl...